3D-PRINTED SOLUTIONS FOR INDUSTRIAL USE.
3D printing in practical industrial use offers clear and decisive advantages: High flexibility, rapid prototype and functional type development and cost- and time-efficient production, even with complex geometries and high load requirements. Thanks to material-, resource- and time-saving production and the ability to manufacture components directly on site, the technology also contributes to sustainability and the strengthening of local supply chains.
Whether individual one-off items, small series, operating aids, tools or spare parts - 3D printing with innovatiQ's industrial printers enables innovative, economical, adaptable and resource-saving production. This is clearly illustrated by the following examples from the practical experience of some of our customers.
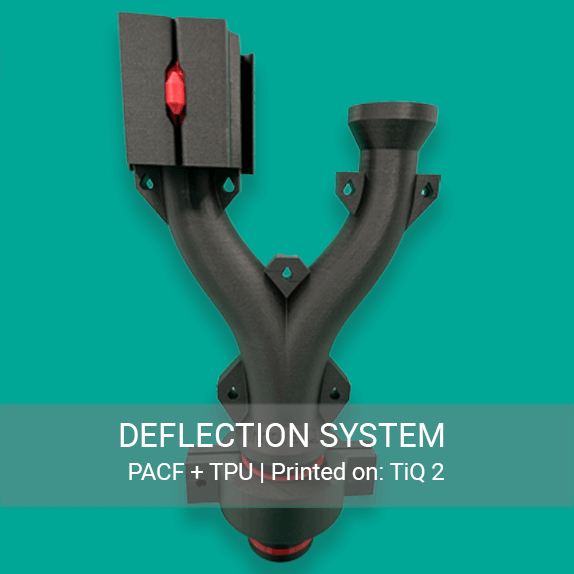
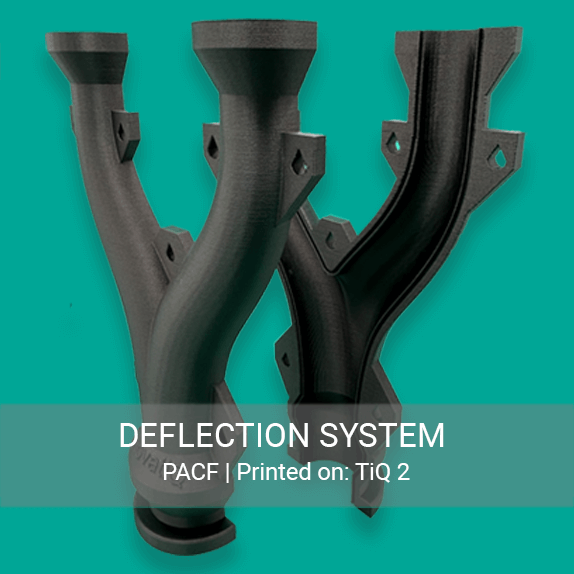
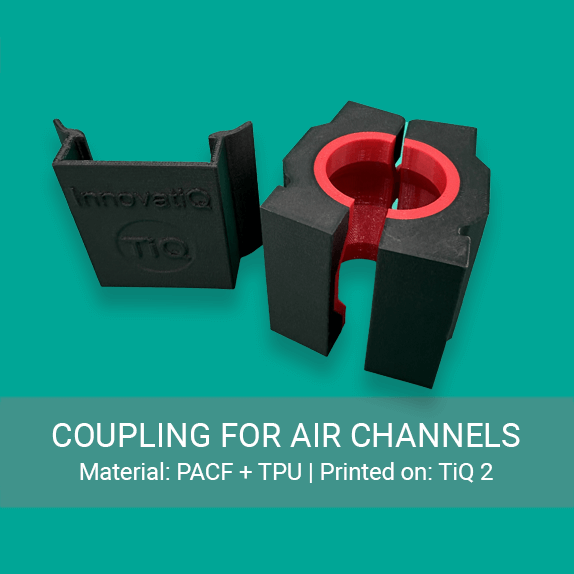
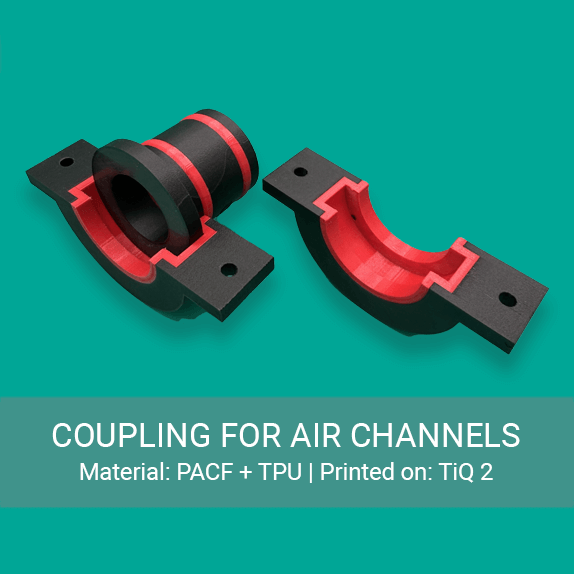
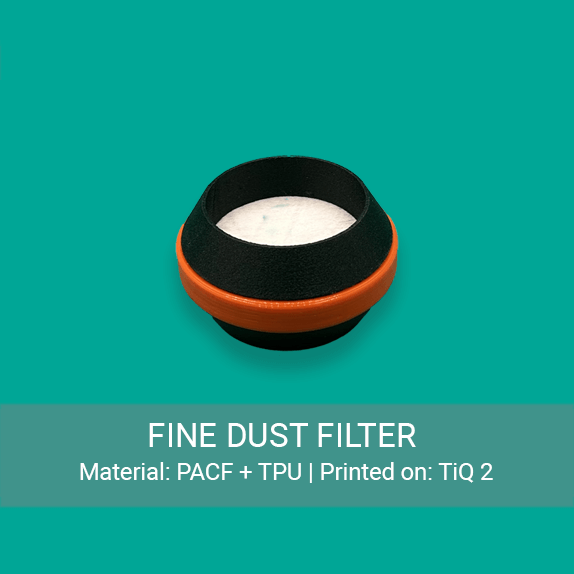
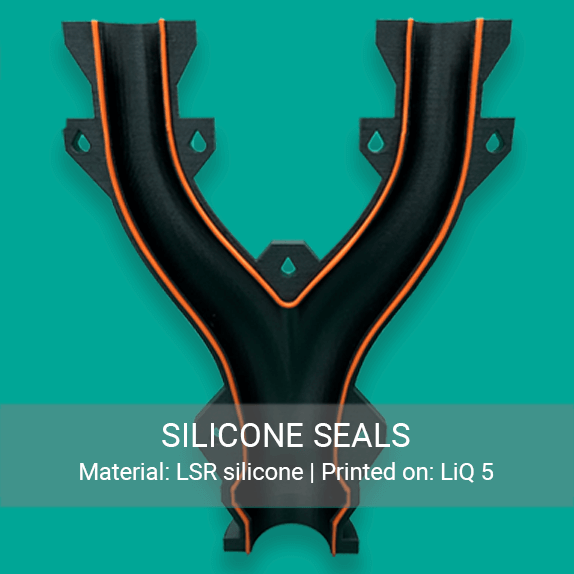
MECHANICAL & PLANT ENGINEERING:
AIR FLOW CONTROL IN COMBINED PRODUCTION TECHNOLOGY
These topology-optimized components of an exhaust air duct printedon innovatiQ printers are used for the targeted discharge of exhaust air in an industrial production facility. By using additive manufacturing technologies, the geometry of the exhaust air duct was optimally adapted to the existing tight installation conditions. An integrated and replaceable fine dust filter, as well as all connecting and coupling pieces, were manufactured using the TiQ 2 with PA-CF . A special feature of this application example is the multi-component printing: the air-conducting components were printed with the TiQ 2 FDM printer , while the integrated seals in all plug connections were produced from flexible TPU in the same print run with the second print head. The seals between the two-part main guide channels were produced from silicone on the innovatiQ LiQ 5 silicone printer.
The components for the narrow, difficult-to-access installation site would have been difficult or impossible to produce using conventional manufacturing methods. Thanks to the choice of suitable, heat-resistant materials , the 3D-printed solution guarantees high thermal and mechanical resilience even in long-term use.
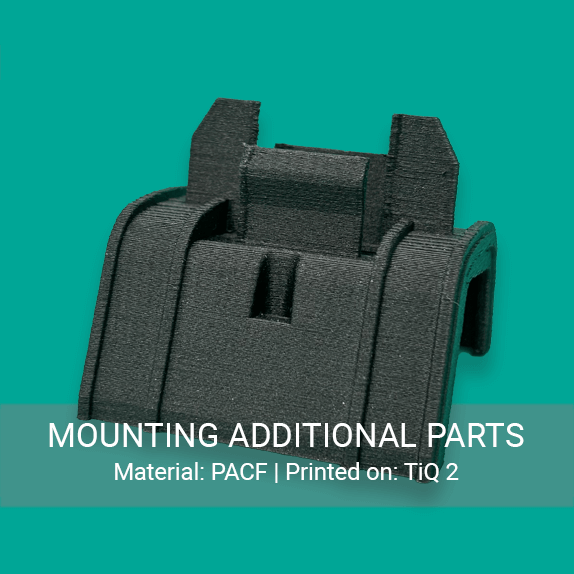
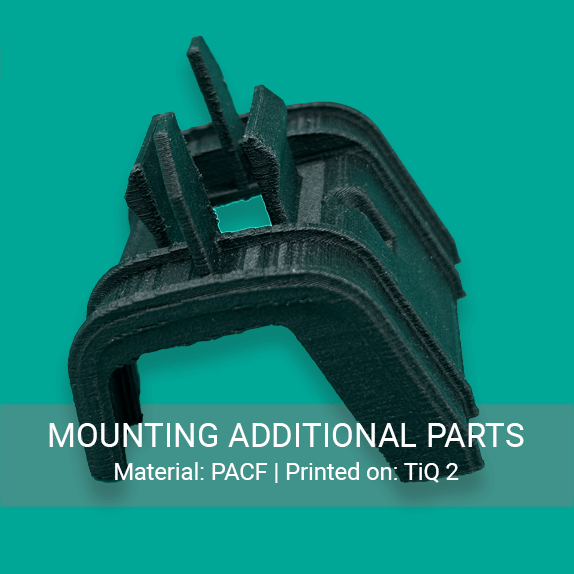
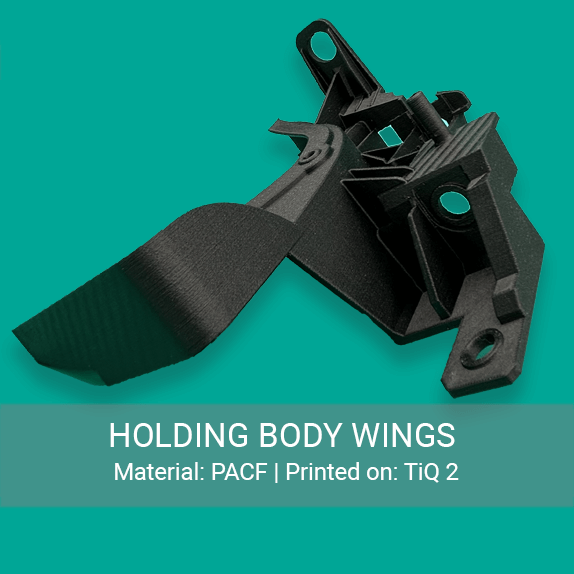
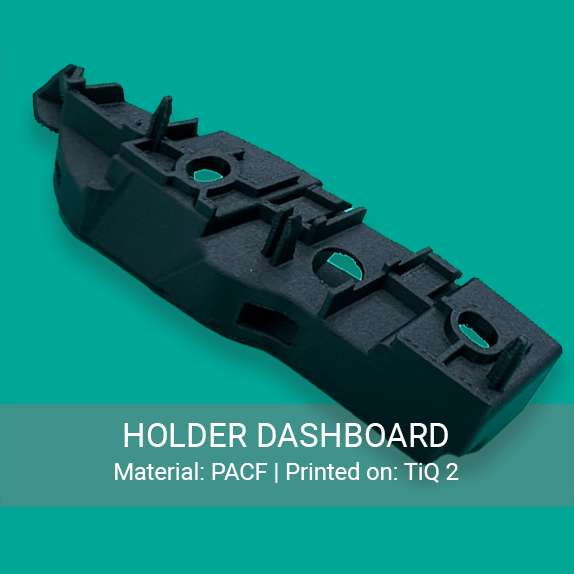
AUTOMOTIVE:
SPARE PARTS & CUSTOM-MADE PRODUCTS
3D printing is revolutionizing the automotive industry - through high flexibility in manufacturing and efficiency in production. In-house additive manufacturing enables companies to use innovative and resource-saving manufacturing processes that meet the increasing demands of industrial production. Flexibility plays a central role: with 3D printing, prototypes, spare parts or individual components can be produced in the shortest possible time - without complex tools or long lead times. 3D printing works efficiently with materials - lighter components, including those with complex yet highly resilient structures, help to reduce vehicle weight. In the automotive industry, 3D printing combines technological innovation with sustainable action - and is thus helping to shape the mobility of tomorrow.
There are also major advantages in the aftermarket sector: Spare parts that are no longer available , such as the brackets for body and add-on parts from our application and practical examples, can be reproduced quickly and cost-effectively in small quantities.
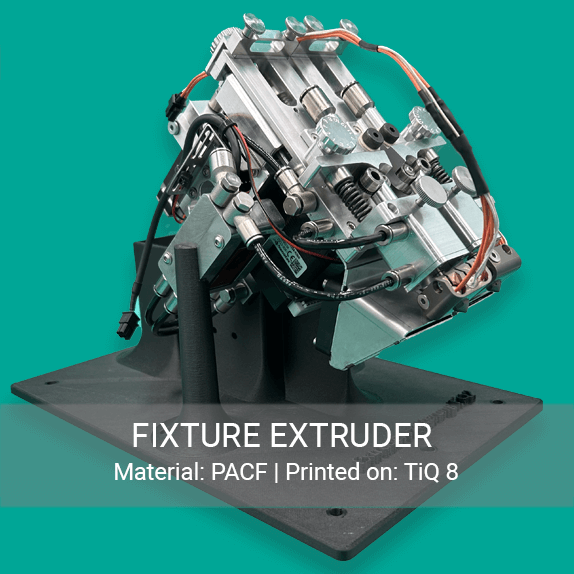
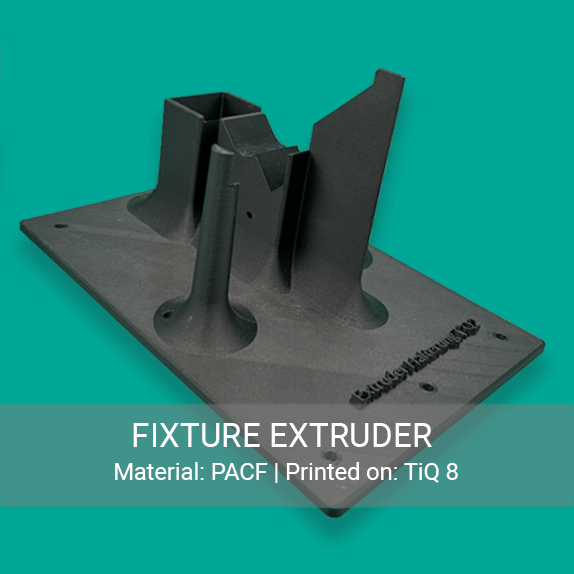
AUTOMATION:
AUTOMATIC CREATION OF RECORDINGS AND MATERIAL CARRIERS
From the need to the finished printed tool or component holder in a short time: innovatiQ recommends fixturemate as a particularly useful addition to an industrial innovatiQ 3D printer because it optimizes precisely the part of the workflow that has been a resource and time trap for many companies to date: the fast and flexible design of fixtures (e.g. assembly aids, test fixtures or grippers). It is aimed at both CAD experts and users without in-depth CAD knowledge and enables the quick and easy design of assembly, measuring, welding and test fixtures in just a few minutes.
This provides an efficient and user-friendly solution for designing individual fixtures in an industrial environment. The combination of automated design processes, optimization for 3D printing and an intuitive user interface enables companies to shorten their development times, reduce costs and increase flexibility in production.
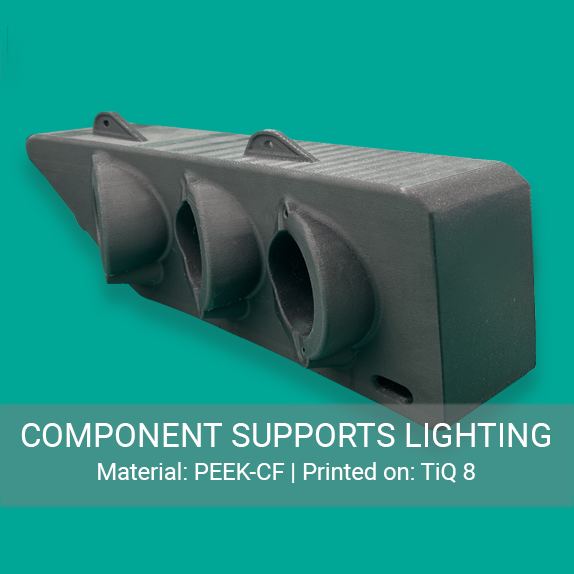
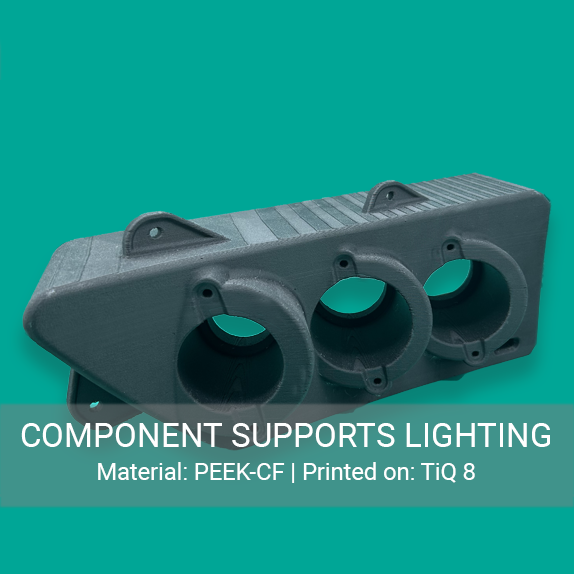
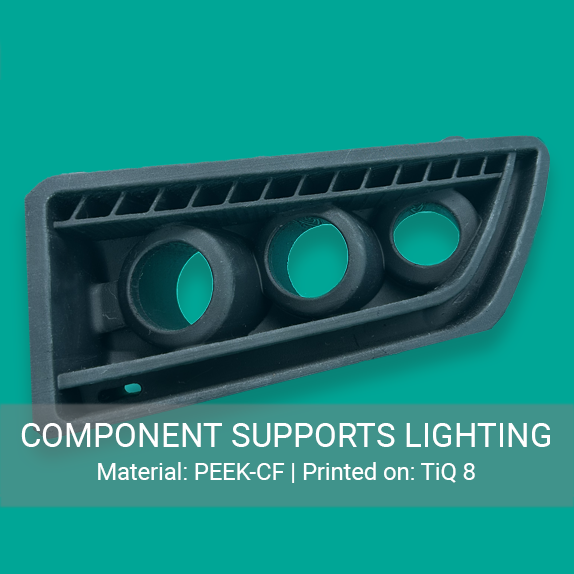
AUTOMOTIVE:
COMPONENT CARRIER FOR LIGHTING OF SPECIAL VEHICLES
The special vehicle manufacturer's part carrier serves as a load-bearing structural component for securely and precisely mounting lighting units, LED modules, indicators and auxiliary headlights in special vehicles such as emergency, rescue or military vehicles. The component was manufactured from fiber-reinforced PEEK-CF using the innovatiQ TiQ 8 in an industrial FDM 3D printing process. Due to the small quantities with individual installation positions on the vehicles, 3D printing enables cost-effective and fast implementation in this case.
Features:
-
Individual geometry for the respective specific vehicle contours or installation situations
-
Integrated cable ducts and fastening points for simplified installation and secure cable routing
-
Lightweight construction combined with high mechanical stability
-
Temperature and UV-resistant material for outdoor use
-
Reduced number of parts due to functional integration (e.g. holder, seal seat, plug connections)
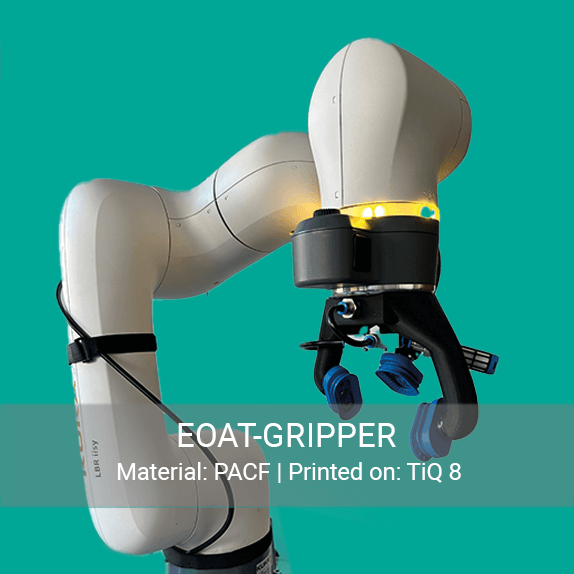
AUTOMATION:
EOAT-GREIFER
This EOAT (end-of-arm tool) mirror gripper, which was manufactured on an innovatiQ TiQ 2 3D printer, is used in the automated production process of an automotive supplier. The gripper is specially designed to grip exterior mirror housings safely and gently. The customized shape and special gripping surfaces with soft suction cups ensure safe, fast and damage-free handling.
3D printing on the innovatiQ TiQ 2 offered numerous advantages here. It enables a high degree of design freedom, allowing the gripper to be adapted precisely to the geometry and requirements of the respective workpiece. The low weight of the printed components improves the robot's dynamics and energy efficiency. The innovatiQ TiQ 2 is designed for industrial applications and can process technical carbon fiber-reinforced filaments excellently, as in this example, resulting in stable, durable gripper solutions.
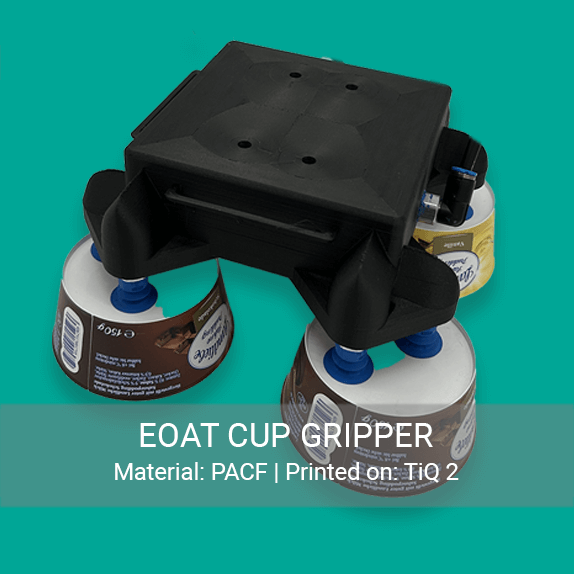
AUTOMATION:
END OF ARM TOOLS
This EOAT (end-of-arm tool) yoghurt cup gripper, which was manufactured using industrial 3D printing on an innovatiQ TiQ 2, is used by a food manufacturer for the automated handling of lightweight, thin-walled plastic packaging, such as yoghurt cups. The gripper performs a central function in the sorting and filling line: it grips the cups precisely, lifts them, positions them correctly and then transfers them to the downstream process stations - for filling, capping and labeling, for example. It is particularly important that the sensitive packaging is not deformed or damaged. The gripper must therefore not only be reliable, but also extremely gentle on the material.
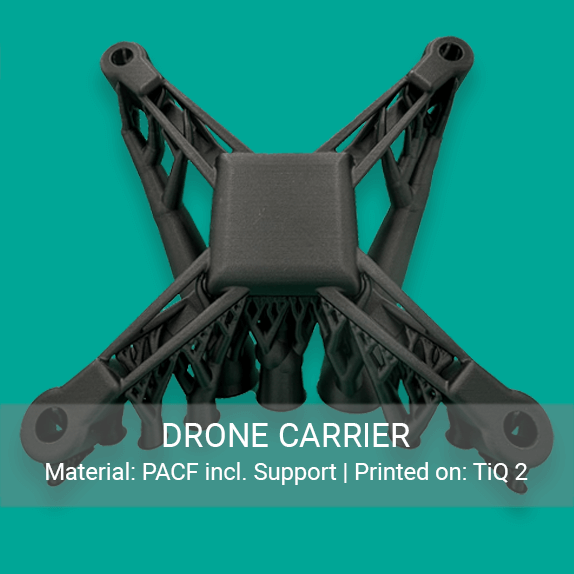
OTHER INDUSTRIES:
DRONE CARRIERS
This 3D-printed drone carrier, manufactured on the innovatiQ TiQ 2, is a lightweight, stable structural component for use in UAV systems. It connects central components such as rotor arms, batteries and sensors and ensures stability during flight.
Thanks to the industrial 3D printing process, it was possible to design the carrier in a topology-optimized way - material was only used where it was mechanically necessary. As a result, the carrier is particularly light, but resilient. In addition, functional elements such as cable ducts, brackets or plug-in connections are directly integrated, which saves assembly work. The carbon fiber-reinforced filament PACF, which offers high strength and low weight, was used for printing. The TiQ 2 enables precise and low-distortion production, ideal for functional UAV components.
The drone carrier shows how 3D printing efficiently combines flexibility, lightweight construction and functionality in one component - ideal for prototyping, small series or individual adaptations in drone construction.
SOLUTIONS & APPLICATION EXAMPLES:
innovatiQ's 3D printers have proven themselves in numerous industrial applications over the long term and are now an integral part of modern manufacturing processes in many companies. Thanks to their reliability, precision and high performance, they are convincing both in daily operation and in specialized areas of application. Whether in series production, product development or equipment construction - innovatiQ systems offer sophisticated solutions for a wide range of requirements. The variety of applications for customers from sectors such as the automotive industry, mechanical engineering, medical technology and packaging technology impressively demonstrates how widely applicable and economically viable industrial 3D printing can be. With an in-house 3D printer, prototypes, functional parts, devices and individual equipment can not only be produced faster and more cost-effectively, but can also be flexibly adapted to new requirements. This eliminates long delivery times from external manufacturers, which shortens development cycles and significantly increases responsiveness in production.